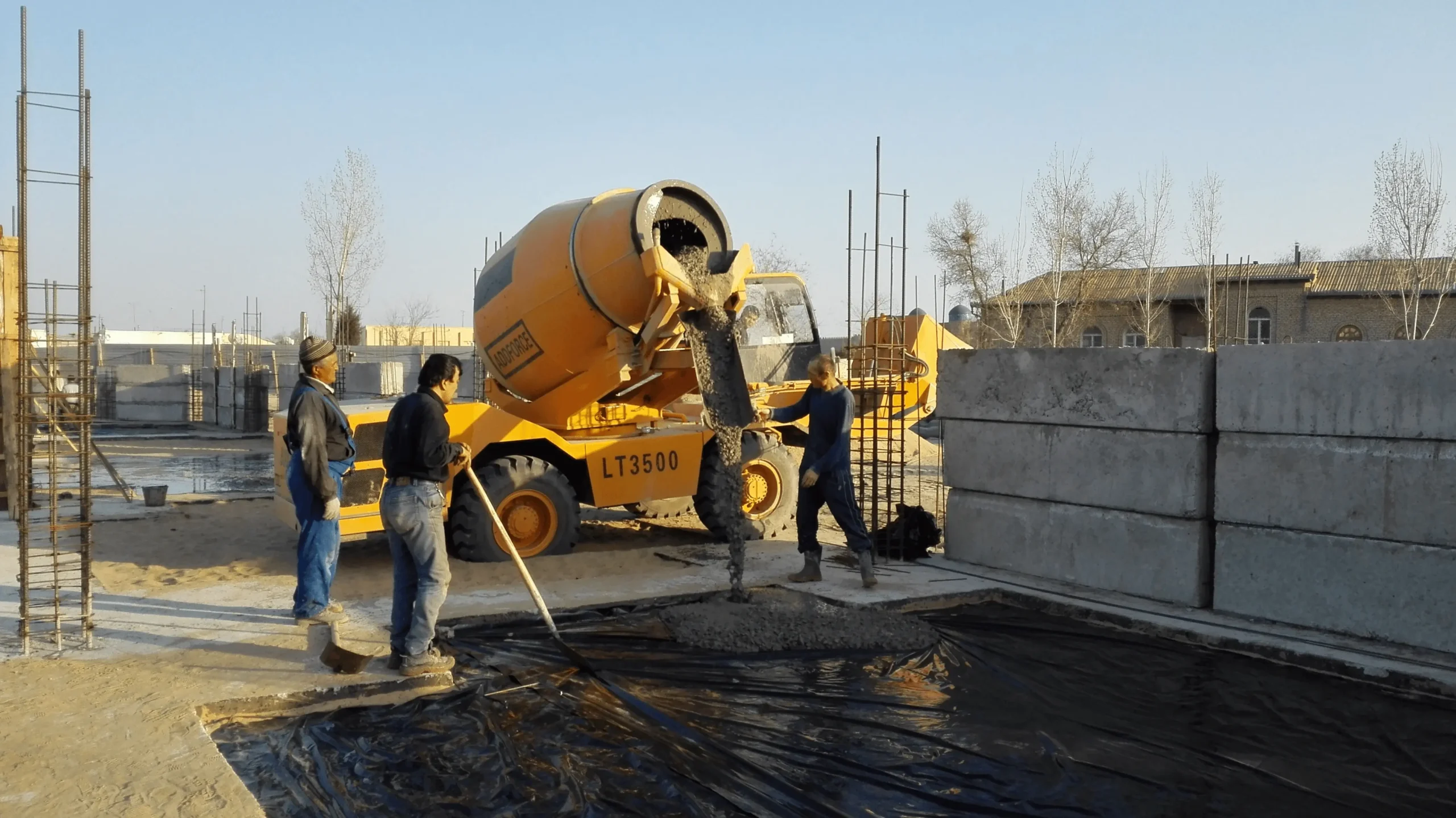
Concrete mixers play a fundamental role in the construction industry, facilitating the production of high-quality concrete for a myriad of projects. From the humble beginnings of horse-drawn wooden barrel mixers to the cutting-edge technologies of modern concrete mixer trucks, the evolution of concrete mixing equipment has revolutionized construction practices worldwide. In this overview, we delve into 25 fascinating facts about concrete mixers, spanning historical milestones, technological innovations, industry insights, and environmental considerations. Join us as we explore the key aspects of this essential component of construction, from its humble origins to its pivotal role in shaping the future of infrastructure development.
Spinning Speed: Concrete mixer drum rotation speed is crucial for achieving a homogeneous mixture. During mixing, the drum typically rotates at a slower speed of 12-18 RPM (revolutions per minute) to thoroughly blend the ingredients. However, during discharge, a faster rotation speed of 25-30 RPM is necessary to ensure consistent pouring and prevent segregation of the mix. This controlled rotation speed is essential for maintaining the quality and consistency of the concrete being produced, whether it’s for small-scale projects or large construction sites.
Early Design: The construction industry witnessed a revolution in concrete production with the invention of the first concrete mixer. While the exact year and inventor hold some debate, by 1904, horse-drawn mixers were already at work. These early designs, most notably patented by Richard Bodlaender in 1904, marked a significant leap forward from traditional hand-mixing methods. Bodlaender’s portable concrete mixer, dubbed the “Mortar Mixer,” featured a horse-drawn cart with a large rotating drum in place of the front wheels. Inside the drum, paddles churned the concrete mix, achieving a level of efficiency and consistency previously unattainable. This pioneering invention, with its estimated 12 cubic meter (423 cubic feet) capacity (considering the size of horse-drawn carts), paved the way for future advancements in concrete technology. It laid the foundation for the modern concrete mixer trucks and stationary mixers we rely on today, machines that continue to evolve and push the boundaries of construction capabilities.
Concrete Hauling Powerhouses: Concrete mixer trucks come in various sizes, with some reaching capacities of up to 12 cubic meters (423 cubic feet). These large-capacity trucks play a crucial role in transporting significant amounts of concrete, optimizing logistics and reducing trips for mega-projects requiring vast quantities of concrete within a tight timeframe.
Mini Marvels: Countering the dominance of large concrete mixers, portable models offer a vital solution for small-scale construction projects, DIY use, and remote locations. With drum capacities typically starting around 6-8 liters (2-3 cubic feet), these compact mixers provide maneuverability and are ideal when large-scale equipment is impractical.
Electric Avenue: The advent of electric-powered concrete mixers marked a significant milestone in the evolution of concrete technology. In 1932, the Koehring Company developed the first electric-powered concrete mixer, ushering in a new era of efficiency and sustainability in construction. Electric mixers offer several advantages over their diesel-powered counterparts, including lower emissions, reduced noise pollution, and greater versatility in indoor and urban environments.
Pumping Power: Modern concrete mixer trucks are equipped with advanced pumping systems that enable them to deliver concrete over long distances with precision and efficiency. With the aid of a boom and pump mechanism, these trucks can pump concrete horizontally over distances exceeding 150 meters (492 feet). This capability eliminates the need for manual labor and heavy machinery to transport concrete to elevated or hard-to-reach areas, streamlining the construction process and enhancing productivity on-site.
World’s Tallest Poured Concrete Structure: The construction of the Burj Khalifa in Dubai, United Arab Emirates, stands as a testament to the monumental scale of modern engineering feats. During its construction, over 330,000 cubic meters (1.17 million cubic feet) of concrete were utilized, making it the world’s tallest poured concrete structure. This staggering volume of concrete highlights the crucial role of concrete in shaping contemporary skylines and pushing the boundaries of architectural innovation.
Record-Breaking Continuous Pour: According to Guinness World Records, the record for the longest continuous concrete pour belongs to PS-Co. (Iran), achieved in Tehran, Iran, between March 1-6, 2018. This pour lasted 5 days, 4 hours, and 11 minutes. The record for the largest volume of continuous concrete pour was set on March 27, 2024, in Riyadh, Saudi Arabia, by Mohammad Abdulaziz Al-Habib Real Estate Company. This pour poured 69,824.87 cubic meters (2,465,842 cubic feet) of concrete.
Mixing Power: The drum of a concrete mixer truck exerts considerable force during the mixing process to ensure a uniform blend of ingredients. With a mixing force of up to 100,000 Newtons (22,481 pounds of force), these robust drums effectively agitate the concrete mixture, preventing segregation and achieving optimal consistency. This mixing power is essential for producing high-quality concrete that meets the structural and performance requirements of diverse construction applications.
Global Concrete Guzzler: China’s voracious appetite for concrete solidifies its position as the world’s largest consumer of this essential construction material. Annually, China consumes over 2.3 billion metric tons of concrete, accounting for more than half of the global total. This staggering demand reflects China’s rapid urbanization, infrastructure development, and construction boom, driving the country’s construction industry to new heights while shaping the global concrete market.
Mixing Time Matters: The optimal mixing time for concrete varies depending on factors such as mix design, ingredients, and environmental conditions. Typically ranging between 1.5 to 3 minutes, this critical phase ensures thorough blending of cement, aggregates, water, and admixtures to achieve the desired consistency and strength. Overmixing can lead to excessive air entrainment or loss of workability, while undermixing may result in poor cohesion and uneven distribution of ingredients.
Water Weight: Water plays a crucial role in the hydration process of concrete, comprising approximately 15-20% of the total weight of a concrete mix. Its precise measurement and addition are vital for achieving the desired workability, setting time, and final strength of the concrete. Too much water can weaken the mixture and increase shrinkage, while insufficient water can hinder hydration and compromise durability.
Aggregate Arithmetic: Aggregates, including sand, gravel, and crushed rock, constitute the bulk of a concrete mix, typically comprising 60-80% of the total weight. These granular materials provide structural stability, reduce shrinkage, and enhance the overall strength of concrete. Proper grading, proportioning, and quality control of aggregates are essential for optimizing the mix’s performance and durability in various construction applications.
Cement Savvy: Cement serves as the binding agent in concrete, typically accounting for around 10-15% of the total weight of the mix. Its primary role is to chemically react with water to form a paste that binds the aggregates together and hardens over time. Different types of cement, such as Portland cement, blended cement, and specialty cements, offer specific properties and performance characteristics tailored to diverse construction needs.
Truck Turner: Fully loaded concrete mixer trucks can weigh over 40 metric tons (44 US tons), making them heavy-duty vehicles capable of transporting substantial quantities of concrete. The weight of the loaded truck must be carefully managed to comply with road regulations and ensure safe operation. Proper distribution of the load, tire pressure monitoring, and adherence to weight limits are crucial for preventing accidents and preserving road infrastructure.
Drum Diameter Diversity: Concrete mixer drum diameters vary depending on the size and type of mixer, ranging from approximately 1 meter (3.3 feet) for smaller truck mixers to over 3 meters (10 feet) for large central mixing plants. The diameter of the drum influences factors such as mixing capacity, discharge speed, and overall vehicle dimensions. Engineers carefully design drum dimensions to optimize performance and efficiency while meeting transportation regulations.
Mixing on the Move: The introduction of truck-mounted concrete mixers in Germany in the early 1900s revolutionized construction logistics by enabling on-site mixing and delivery of fresh concrete. These mobile units eliminated the need for stationary mixing plants and facilitated just-in-time delivery, reducing construction time and costs. Truck-mounted mixers remain indispensable tools in modern construction, offering flexibility, efficiency, and versatility in various project settings.
Self-Loading Champions: Some concrete mixer trucks are equipped with a front-loading bucket mechanism that allows them to self-load aggregates, further enhancing efficiency and productivity on job sites. This innovative feature eliminates the need for additional equipment or manual labor to load materials, streamlining the mixing process and reducing turnaround time. Self-loading mixer trucks are particularly advantageous for remote or inaccessible locations where external loading facilities are limited.
The Great Rotation: Continuous rotation of the concrete mixer drum is essential for preventing segregation of ingredients and ensuring a uniform mix. The constant agitation maintains the homogeneity of the concrete mixture throughout transportation and delivery, minimizing the risk of particle settling or separation. Engineers carefully control the speed and direction of drum rotation to optimize mixing efficiency and maintain quality standards.
Safety First: Modern concrete mixer trucks are equipped with a range of safety features to protect operators, workers, and bystanders on construction sites. These include alarms, warning lights, backup cameras, and automatic shutoff systems that activate in case of emergencies or malfunctions. Additionally, safety protocols, training programs, and regular equipment inspections are integral components of ensuring safe operation and accident prevention in the concrete industry.
Cleaning Crew: After each use, thorough cleaning of the concrete mixer truck drum is essential to prevent hardened concrete buildup, which can compromise performance and reliability. Using high-pressure water jets, brushes, and cleaning agents, operators meticulously remove residual concrete from the drum’s interior surfaces. Regular maintenance and cleaning procedures help extend the lifespan of the equipment, minimize downtime, and ensure consistent quality in concrete production.
Environmental Efforts: Recognizing the environmental impact of concrete production, modern concrete mixer trucks are designed with features to reduce emissions and improve fuel efficiency. Advanced engine technologies, emission control systems, and alternative fuel options, such as natural gas and electric power, help mitigate the carbon footprint of concrete transportation. Sustainable practices, such as route optimization and idle reduction strategies, further contribute to minimizing environmental impact in the construction industry.
The Future is Green: Ongoing research and development efforts focus on developing sustainable concrete mixes with lower carbon footprints and increased use of recycled materials. Innovations in alternative binders, supplementary cementitious materials, and eco-friendly additives aim to improve the environmental sustainability of concrete production without compromising performance or durability. These initiatives align with global efforts to address climate change and promote more sustainable practices in construction and infrastructure development.
A Global Industry: The concrete mixer market is a dynamic and rapidly growing sector expected to reach a value of over USD 10 billion by 2025. This significant growth is driven by increasing construction activities worldwide, urbanization trends, infrastructure development projects, and technological advancements in concrete mixing equipment. Market players continue to innovate and diversify their product offerings to meet evolving customer demands and regulatory requirements in a highly competitive industry landscape.
Concrete Careers: The concrete industry offers diverse employment opportunities, employing millions of people worldwide in various roles across the supply chain. From mixer truck drivers and plant operators to engineers, technicians, and project managers, a wide range of skill sets and expertise are required to support concrete production and construction activities. Training programs, apprenticeships, and professional development opportunities help cultivate a skilled workforce and promote career advancement within the dynamic and rewarding field of concrete technology.
Concrete Mixers FAQs:
What are the different types of concrete mixers and which one should I choose for my project?
There are two main categories of concrete mixers: drum mixers and pan mixers.
Drum mixers are the most common type, with a rotating drum that mixes the concrete ingredients. They come in two varieties: tilting drum mixers and reversing drum mixers. Tilting drum mixers have a drum that tilts to discharge the concrete, while reversing drum mixers have a drum that rotates in one direction to mix and then reverses to discharge. Drum mixers are available in sizes suitable for both small DIY projects and large construction sites.
Pan mixers have a rotating pan with stationary blades that mix the concrete. They are typically used for precast concrete applications where a more controlled mixing process is required.
Choosing the right mixer depends on the size and scope of your project. Here’s a breakdown:
Small DIY projects (sidewalks, patios): A small electric or gas-powered tilting drum mixer with a capacity of 3.5 to 7 cubic feet (100 to 200 liters) is ideal.
Medium-sized projects (driveways, foundations): A larger electric or gas-powered tilting drum mixer with a capacity of 7 to 14 cubic feet (200 to 400 liters) is suitable.
Large projects (building slabs, pools): Consider a concrete mixer truck for projects requiring a continuous supply of concrete. These are typically rented by the hour and come in various capacities.
How long should I mix concrete for?
The optimal mixing time for concrete depends on the specific mix design and the size of the batch. However, as a general guideline, you should mix concrete for between 1.5 to 3 minutes. Here’s a breakdown:
Shorter mixing times (around 1.5 minutes): Acceptable for smaller batches using a well-balanced mix design.
Longer mixing times (up to 3 minutes): Recommended for larger batches, colder temperatures, or stiffer mixes.
Overmixing concrete can actually trap air bubbles and weaken the final product. Aim for a homogenous mixture where all ingredients are thoroughly combined without any dry pockets.
How do I clean a concrete mixer?
Cleaning a concrete mixer is crucial to prevent hardened concrete buildup and ensure its smooth operation. Here’s the process:
Turn off the mixer and unplug it (if electric).
Immediately after use, add water to the drum and rotate it for a few minutes. This will loosen up any fresh concrete residue.
Discharge the wash water. You can repeat this step with clean water if needed.
Use a shovel or scraper to remove any stubborn concrete chunks.
Finally, rinse the drum thoroughly with clean water and leave it to dry completely.
Never use harsh chemicals or solvents to clean a concrete mixer.
What safety precautions should I take when using a concrete mixer?
Always wear personal protective equipment (PPE) such as gloves, safety glasses, and dust mask.
Ensure the mixer is on stable, level ground and properly secured before starting.
Never overload the mixer. Follow the manufacturer’s recommended capacity limits.
Keep children and pets away from the operating mixer.
Be aware of rotating parts and pinch points. Keep your hands clear while the mixer is running.
Turn off the mixer before adding or removing any materials.
Never walk under a raised discharge chute.
How much does it cost to rent a concrete mixer?
The cost of renting a concrete mixer depends on the size, type, and rental duration. Here’s a ballpark range:
Small electric mixers: $30- $50 per day
Larger gas-powered mixers: $50- $100 per day
Concrete mixer trucks: $100- $200 per hour (plus additional charges for concrete and pumping)
It’s always best to contact your local rental companies to get specific quotes for your project requirements.